The Value of Welding WPS: Making Sure High Quality and Safety in Your Jobs
The Value of Welding WPS: Making Sure High Quality and Safety in Your Jobs
Blog Article
Grasping Welding WPS Criteria: Best Practices and Techniques for Top Quality Welds
In the realm of welding, mastering Welding Procedure Spec (WPS) standards is an essential part that directly affects the top quality and honesty of welds. Sticking to these requirements makes certain consistency and reliability in welding results. Nonetheless, achieving quality in welds surpasses just recognizing the criteria; it involves implementing ideal practices and methods that elevate the craft to a level of precision and skill that establishes apart the standard from the outstanding. As we browse through the complexities of welding WPS requirements, revealing crucial understandings and techniques for accomplishing top-tier welds will certainly be critical for welders looking for to stand out in their craft and create welds that stand the examination of time.
Comprehending Welding WPS Specifications
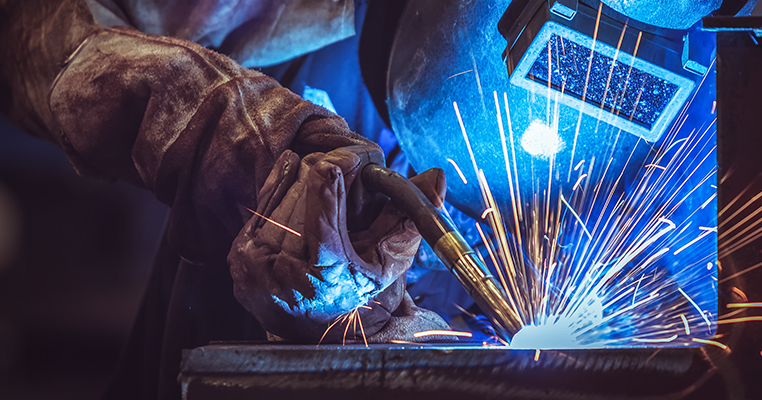
Comprehending WPS criteria is important for welders, assessors, and engineers entailed in welding operations. By following WPS standards, welders can create welds that satisfy the called for mechanical residential or commercial properties and structural honesty. Inspectors count on WPS documents to validate that welding procedures are being complied with properly and that the resulting welds are of high quality. Engineers use WPS requirements to make welding procedures that ensure the durability and reliability of bonded frameworks.

Important Devices for Quality Welds
Understanding welding WPS criteria is vital for welders to effectively make use of the important devices required for creating top quality welds. The type of welding equipment needed depends on the welding procedure being used, such as MIG, TIG, or stick welding. Cable brushes and damaging hammers are necessary for cleaning up the weld joint prior to and after welding to get rid of any type of impurities that might affect the high quality of the weld.
Trick Techniques for Welding Success
To visit here accomplish welding success, one must grasp the crucial strategies necessary for generating high-grade welds. Keeping a stable hand and a steady welding placement throughout the procedure is key to achieving accuracy and consistency in the welds. By understanding these key strategies, welders can elevate the top quality of their job and accomplish welding success.
Ensuring Compliance With WPS Requirements

In addition, welders ought to undergo training to acquaint themselves with the WPS requirements relevant to their job. Regular audits and examinations should be performed to verify that welding activities straighten with the recommended WPS standards. Additionally, keeping in-depth documents of welding parameters, tools calibration, and inspection outcomes is vital for showing conformity with WPS standards - welding WPS. By vigilantly sticking to WPS requirements, welders can guarantee that their job fulfills the required top quality levels and adds to the overall success of the welding project.
Troubleshooting Common Welding Issues
When confronted with common welding problems, determining the origin cause is essential for effective troubleshooting. One widespread trouble is the visibility of porosity in welds, typically created by impurities such as oil, dampness, or corrosion. To resolve this, making certain appropriate cleaning of the base metal before welding and utilizing the correct protecting gas can significantly minimize porosity. An additional problem frequently run into is helpful hints absence of fusion, where the weld fails to correctly bond with the base material. This can originate from insufficient warmth input or inappropriate welding strategy. Readjusting parameters such as voltage, cord feed speed, or take a trip speed can aid enhance fusion. Furthermore, distortion, cracking, and spatter prevail welding difficulties that can be my sources mitigated through correct joint preparation, constant warmth control, and choosing the ideal welding consumables. By extensively recognizing these typical welding concerns and their origin causes, welders can efficiently repair issues and achieve high-quality welds.
Conclusion
Finally, mastering welding WPS criteria requires an extensive understanding of the guidelines, using essential tools, and carrying out key techniques for effective welds. Ensuring conformity with WPS criteria is critical for creating top quality welds and staying clear of common welding concerns. By complying with best techniques and practices, welders can achieve regular and dependable results in their welding projects.
In the realm of welding, mastering Welding Treatment Requirements (WPS) criteria is an essential element that directly influences the quality and honesty of welds.When delving right into the world of welding techniques, a crucial facet to comprehend is the value and ins and outs of Welding Procedure Requirements (WPS) criteria. WPS requirements provide a detailed standard for welding operations, ensuring consistency, quality, and safety and security in the welding process. The type of welding equipment needed depends on the welding procedure being utilized, such as MIG, TIG, or stick welding.Achieving welding success via the proficiency of key techniques demands a comprehensive understanding and adherence to Welding Treatment Specification (WPS) criteria.
Report this page